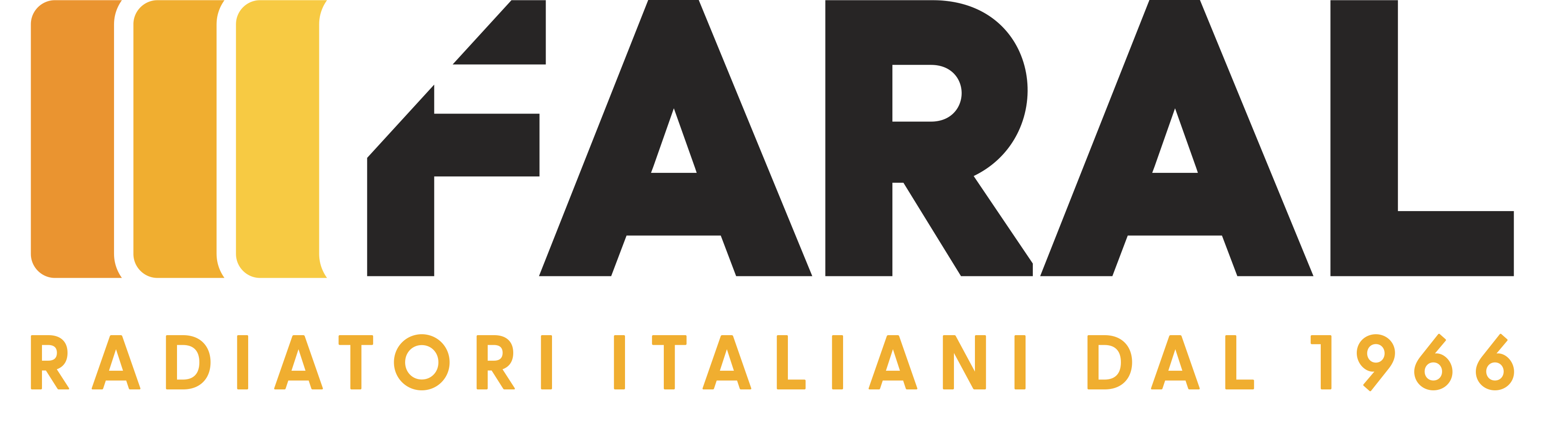
QUALITY
TOTAL QUALITY
Each FARAL radiator is the result of a technological effort that combines aesthetics and performance. Advanced technique, reliability and fully automated productions daily support our experts in a highly developed and automated manufacturing plant where every single activity and every stage of production are managed according to the "FQPES" (Faral Quality and Production Excellence System).
CONTROLS
The procedure of “pressure casting”, conventionally called die-casting, represent a tecnique of producing jets pressing the molten metal in a form where it solidifies quickly. This means uniformity of the pieces, thin, sharp profiles and smooth surfaces. The aluminum alloy is injected to 500 atmospheres and high speed in printing machines before the radiators to pass to the assembly and painting.
Daily cleaning of ovens, visual inspections and spot checks to detect any imperfections are just a few of the products that FARAL must pass the rigorous application of quality control.
MATERIALS
Faral radiators are manufactured with the best alloy quality. The denomination in compliance with Italian regulation which designates the alloy used in FARAL is UNI 5076-74, while according to the European standard EN 46100 the new identification is EN 132/12 Al Si9 Cu. The quality of aluminum alloy, already certified at the time of delivery of the loaves, is constantly monitored with the mass spectrometer. These controls are followed by systematic controls, as well as tests for the determination of the gas content in the molten alloy.
AUTOMATION
Grinding, welding, threading and counter bore are the operations which precede the assembly of the elements in batteries according to the needs of the customer, from 4 up to 15 elements. The high level of automation of these processes, as well as the constant presence of operators with specific tasks of monitoring and control, allow to optimize the level of production quality and to decrease the risks of waste to the subsequent production processes.
PAINTING
FARAL radiators are subject to a process of double coating and stoving plus a series of unique controls that ensure compliance with the timing of each production processing station even in the event of a power failure. This means absolute stability of the characteristics of the finished radiator. Furthermore, the paints used by FARAL for the recoating of its radiators are certified as non-toxic and, therefore, harmless. Those used for the final painting respect the limits established for the coating of toys. This means that in case of fire, the fire resistance of FARAL radiators do not cause vapors or toxic fumes.
CONVERSION
The exclusive cycle of pretreatment of the internal and external surfaces is followed by a complex cycle of high temperature alkaline degreasing, DE oxidation acid and the conversion treatment. In this critical step the aluminum surface is converted into an inert film of aluminum oxide chemically bonded to the product passivating. The maintenance of the control of very strict parameters guarantee the absolute lack of salt residues on the treated pieces as well as the formation and accumulation of gas within the plant.